In the field of intelligent manufacturing, vision-following dispensing machines, with their superior high-precision dispensing capabilities, have become key equipment in industries such as electronics, semiconductors, and medical care. So, exactly how does it achieve micron-level or even nanometer-level dispensing? Its core principle is worthy of in-depth exploration.
I. Visual Recognition System: The "Eyes" of Motion Capture
The visual system of the visual following dispensing machine is composed of an industrial camera, a light source component and an image processor. Industrial cameras capture the surface features of workpieces at high frame rates, and are combined with dedicated light sources such as ring-shaped and back-facing ones to enhance contrast, ensuring the clarity of the target contour. The image processor locates the workpiece coordinates in real time through algorithms such as edge detection and template matching. For example, in the packaging of mobile phone chips, the system can identify a tiny area with a pin spacing of only 0.3mm within 0.1 seconds, and the error is controlled within ±0.01mm.
Ii. Motion Control Module: The "Executor" of Micron-level Displacement
The motion platform composed of the servo motor and the high-density lead screw is the key to achieving accurate displacement. The servo motor receives instructions from the vision system in a closed-loop control mode and, in conjunction with a linear guide rail with a resolution of 0.001mm, drives the dispensing head to move at high speed along the X/Y/Z axes. When a workpiece offset is detected, the motion controller can adjust the trajectory within 20ms to ensure that the error of the glue drop point is less than 5μm, which is equivalent to 1/10 of the diameter of a human hair.
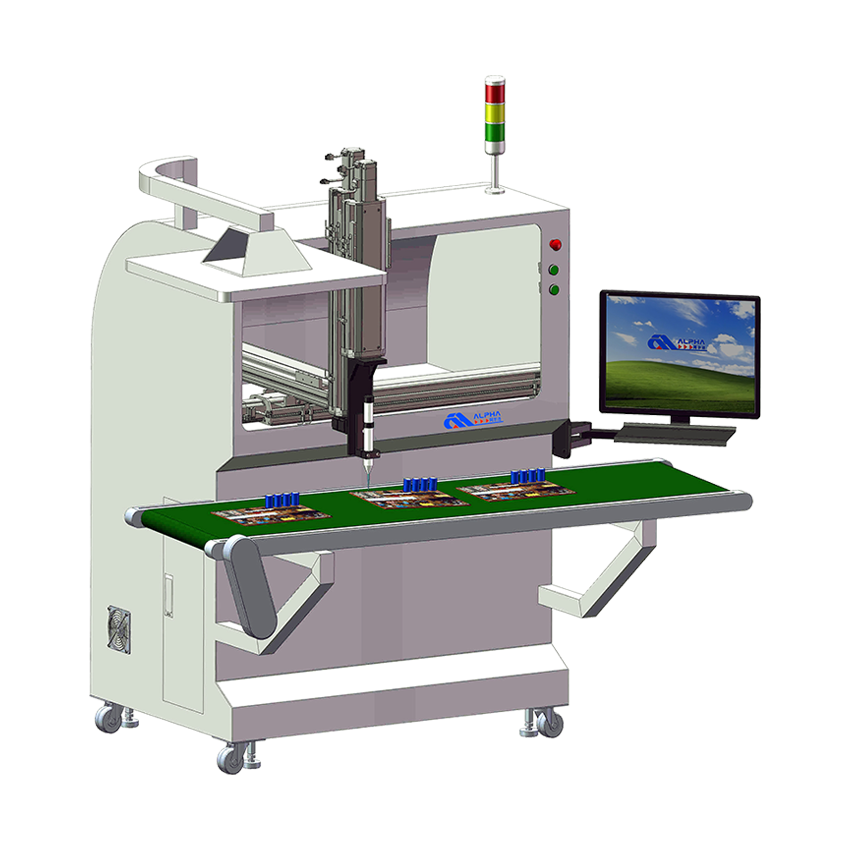
Visual following dispensing machine
Iii. Closed-loop Control of Glue Volume: The "nerve" of Intelligent Regulation
The dispensing machine is equipped with an internal pressure sensor and a flow monitoring device, forming a closed-loop system for glue volume. Take the peristaltic dispensing valve as an example. The sensor monitors the pressure of the dispensing path in real time. If a change in the viscosity of the glue is detected (such as caused by temperature fluctuations), the controller immediately adjusts the dispensing time and air pressure parameters. This dynamic compensation mechanism can control the glue quantity error within ±2%, meeting the ultra-micro dispensing requirement of 0.05nL for Mini LED chips.
Iv. Multi-system Collaboration: The "Intelligent Brain" with Millisecond-level Response
The three major modules of vision, motion and glue volume are deeply coupled through the real-time operating System (RTOS). When the system detects the offset of the workpiece position, the vision module outputs the correction coordinates within 0.05 seconds, the motion module synchronously plans the short path, and the glue quantity module pre-adjusts the glue output parameters. The entire response process is completed within 100ms. This millisecond-level collaborative capability enables the dispensing machine to maintain accurate operation even when the assembly line speed reaches 300mm/s.
V. Industry Application Verification: A Breakthrough from Theory to Practice
In the scenario of ear dispensing for new energy batteries, the visual following dispensing machine dynamically corrects the dispensing trajectory by identifying the deformation of ear folds, reducing the 8% overflow rate of the traditional process to less than 1%. In the field of medical catheter packaging, its nano-level dispensing accuracy has successfully solved the industry problem of catheter blockage caused by glue. These cases confirm the reliability of the technical principle under complex working conditions.
With the iteration of AI algorithms and hardware performance, vision-following dispensing machines are evolving towards adaptive learning. In the future, the system can model through historical data to predict the changing trend of workpieces and further enhance the stability of dispensing. For manufacturing enterprises that pursue high precision, understanding its working principle is not only a prerequisite for technological upgrading but also the key to seizing the high ground of intelligent manufacturing.