In manufacturing fields such as electronics, medical care, and automobiles, visual following coating machines have become key equipment due to their high-precision coating processes. However, the problem of nozzle clogging often leads to production disruptions and even causes coating quality defects. This article starts from the clogging mechanism and provides a systematic solution to help you improve the operational efficiency of your equipment.
I. The Three Main Culprits of Nozzle Blockage
The characteristics of the adhesive can cause curing blockage. Imbalance in the mixing ratio of two-component adhesives, premature awakening of curing agents, or rapid drying of low-viscosity adhesives in high-temperature environments are common causes. For instance, when epoxy adhesive is left standing in an environment above 35℃ for more than 2 hours, its viscosity can increase by 300%, directly blocking micron-sized spray holes.
Residual equipment can lead to mechanical blockage. If the residual colloidal crystals and impurity particles are not cleaned thoroughly, or if the nozzle is in long-term contact with corrosive solvents, causing the inner wall to peel off, mechanical blockage will occur. Data shows that equipment that does not undergo daily deep cleaning has a 47% higher probability of clogging.
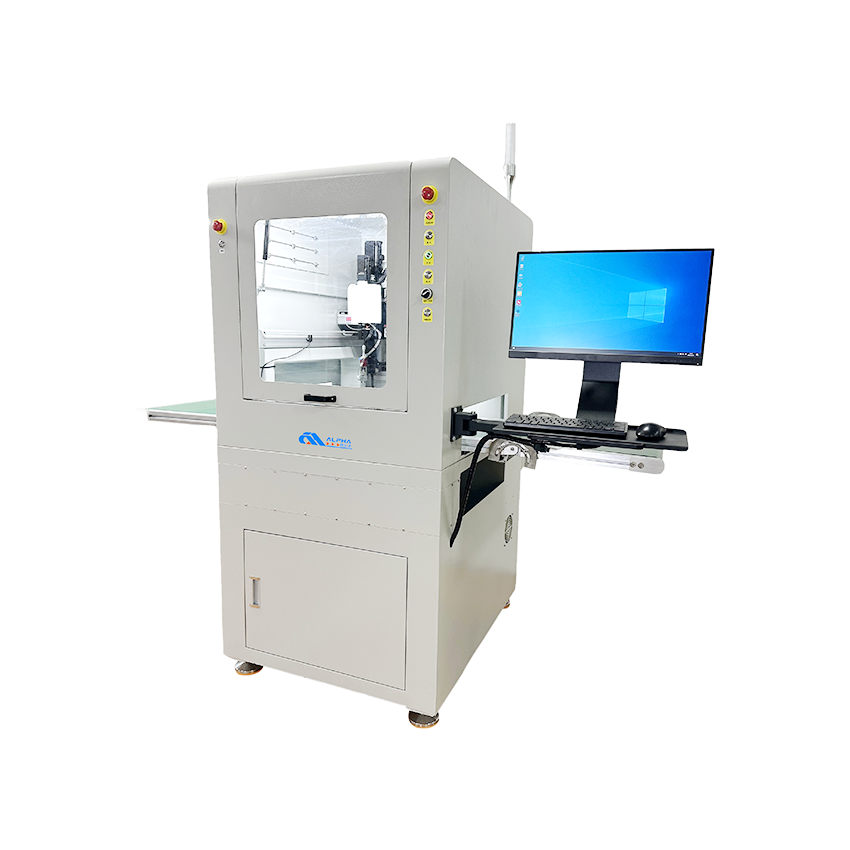
Improper operation can cause a chain reaction. Long-term idling, failure to activate the anti-drying function during the coating gap, or abnormal fluctuations in air pressure parameters will all accelerate the aging of the nozzle. A certain 3C enterprise failed to adjust the air pressure in time, causing the glue to be sucked back and blocked, resulting in a single shutdown loss of over 20,000 yuan.
Ii. Construction of a Hierarchical Prevention System
The "Three Lines of Defense" for material Management
Strictly monitor the shelf life of the glue and conduct a secondary viscosity test before use
The two-component glue adopts a dynamic proportioning system, with an error controlled within ±1.5%
Install a constant-temperature barrel in high-temperature environments to ensure that the temperature fluctuation of the glue is less than 2℃
The standardized equipment maintenance process formulates the "3-2-1" cleaning system:
3-minute pre-cleaning: Rinse immediately with the appropriate solvent after the operation
Two ultrasonic cleanings: Deep cleaning is carried out weekly
One-time disassembly and maintenance: Check the internal wear of the nozzle monthly
The intelligent early warning system is equipped to monitor the resistance of the rubber path in real time through pressure sensors. When the abnormal value reaches the threshold (such as a sudden 15% increase in pressure), an alarm will be automatically triggered and the cleaning program will be linked. After the deployment of this system on a certain automotive electronics production line, the frequency of congestion decreased by 82%.
Iii. The entire process of emergency response to Blockages
Mild blockage: Non-contact unblocking
Solvent immersion: Immerse the nozzle in a dedicated dissolution solution (such as acetone mixed solution) and shake it with ultrasonic waves for 15 minutes
Pulse air pressure unblocking: Set a pulse air pressure of 0.3-0.5MPa and rinse repeatedly every 5 seconds
Severe blockage: High-density disassembly and repair
Calibration before disassembly: Record the installation Angle and parameter Settings of the nozzle
Laser micro-hole cleaning: Utilizing a 532nm pulsed laser to accurately vaporize blockages (with an accuracy of ±0.5μm)
Sealing test: After repair, conduct a 0.8MPa air tightness test and maintain pressure for 30 minutes without leakage
Iv. Verification of Industry Practical Cases
A medical catheter manufacturer once saw its yield rate drop sharply to 68% due to UV glue clogging. By introducing a "glue activation monitoring + intelligent cleaning" system and combining it with a customized nozzle anti-drying kit, it successfully reduced the clogging frequency from three times a week to once a month, saving over 800,000 yuan in maintenance costs annually.