In manufacturing scenarios such as electronic chip packaging and new energy battery modules, the thermal paste coating machine undertakes the core task of evenly coating the heat dissipation layer. However, as the operation time accumulates, problems such as carbonization of the heat dissipation paste and condensation of impurities are prone to cause nozzle blockage and decline in coating accuracy. This article helps enterprises maximize equipment efficiency through standardized cleaning processes and periodic maintenance plans.
I. Step-by-step cleaning process: Build a comprehensive cleaning system
1. Clean quickly after daily work
Pre-rinse stage: 50% isopropyl alcohol dilution solution is selected as the cleaning agent. The rubber circuit system is rinsed with 0.5MPa pulse air pressure circulation for 30 seconds. Combined with the spiral scouring design on the inner wall of the pipeline, more than 90% of the residual paste is effectively stripped off. Nozzle activation treatment: Immerse the nozzle assembly in a 40℃ ultrasonic cleaning tank, use 40kHz high-frequency oscillation waves to break the solidified paste crystals, and use a dedicated filter screen to filter out the detached impurities to ensure the unobstructed spray holes. Gas path drying protection: Use nitrogen with a purity of ≥99.99% for gradient purging (pressure increases from 0.3MPa to 0.6MPa) to remove residual moisture and prevent oxidation and rusting of metal parts.
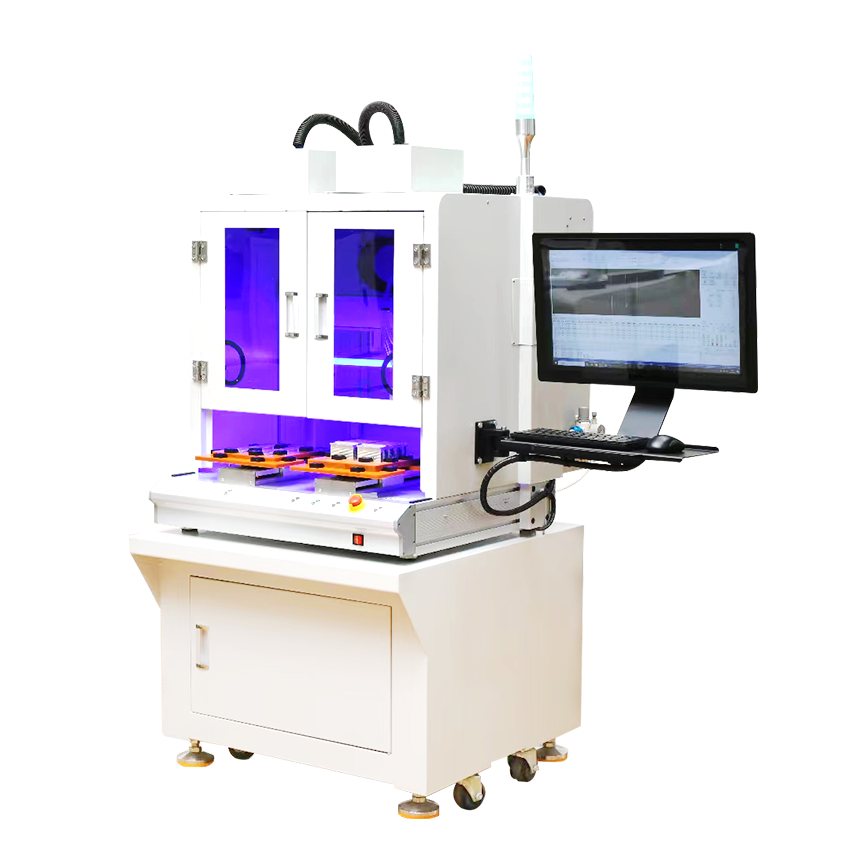
2. Weekly in-depth disassembly and maintenance
Core component disassembly: Follow the principle of "pressure relief first, then disassembly", use special tools to separate the nozzle, metering pump and mixing pipe assembly, and check the compression deformation of the sealing parts (standard value < 0.2mm). Chemical immersion process: Immerse the disassembled parts in a solution of acetone: ethanol in a ratio of 3:2, and use a magnetic stirrer (at a speed of 200rpm) to accelerate the dissolution. For stubborn carbonized layers, the process can be extended to 1.5 hours. Micro-level inspection: Use a 500x industrial microscope to observe the inner wall of the spray hole, mainly to check for impurities with a diameter of less than 5μm adhering, and ensure that the surface roughness Ra of the flow channel is ≤0.8μm.
3. Monthly system calibration and reinforcement
Pressure integrity test: Apply 1.2 times the rated pressure to the rubber circuit system (if the conventional working pressure is 0.8MPa, then the test pressure is 1.0MPa), hold the pressure for 5 minutes, and monitor the pressure drop (allowable value < 0.05MPa). Coating accuracy calibration: By scanning the standard fixture coating with a 3D profilometer and comparing it with the preset thickness (±0.01mm tolerance), the motion parameters are automatically corrected to compensate for mechanical wear. Maintenance of moving parts: Apply HT-100 high-temperature grease (dropping point ≥300℃) to the lead screw and guide rail, and use a quantitative grease injection gun to control the single injection amount at 0.3g/cm.
Ii. Industry Practice Verification: Quantify maintenance benefits
After a certain semiconductor packaging enterprise applied the standardized solution, the equipment operation and maintenance data improved:
Nozzle clogging frequency: Reduced from 7 times per month to 0.5 times (annual downtime cost savings of approximately 320,000 yuan)
Coating defect rate: Decreased from 3.2% to 0.8% (corresponding to an annual increase of 120,000 pieces of chip modules)
Equipment life cycle: Extended from 5 years to 8 years (converted to an average annual asset utilization rate increase of 60%)
Iii. Key Points for maintaining Risk prevention and control
Red line for solvent use: It is strictly prohibited to use strong solvents such as toluene and xylene to avoid damaging PEEK material components
Dual verification of drying: Confirmed by a humidity sensor (residual humidity < 5%) and an infrared thermal imager (uniformity of component surface temperature < 3℃)
Digital management: The EAM system is adopted to record maintenance data and automatically push early warnings for consumable replacement (such as triggering when the compression of the seal remains at 20%).
By following the "prevention - detection - repair" trinity maintenance strategy, enterprises can increase the comprehensive efficiency (OEE) of the thermal paste coating machine to more than 92%. It is recommended to combine the equipment operation logs and dynamically optimize the maintenance cycle parameters to achieve accurate operation and maintenance in the intelligent manufacturing scenario.