Automatic screw machines play a significant role in modern industrial production. They achieve the automatic tightening of screws through an orderly process, thereby enhancing production efficiency. Its working principle mainly revolves around the key links of screw supply, transportation and tightening.
Screw supply is a step in the operation of an automatic screw machine. Under normal circumstances, an automatic screw machine is equipped with a screw silo, and the screws will be centrally placed in the silo. The design of the silo can ensure that the screws are arranged in a certain pattern. Common types include vibrating disc silos. The vibrating disc generates vibration through the vibrating motor at the bottom. During the vibration process, the screws slide along a specific track. Meanwhile, a directional mechanism is set on the track, allowing the screws to enter the conveying track in a uniform posture (such as head up and threaded end forward) one by one. This arrangement method prepares for subsequent conveying and tightening, avoiding problems such as blockage caused by disordered screws.
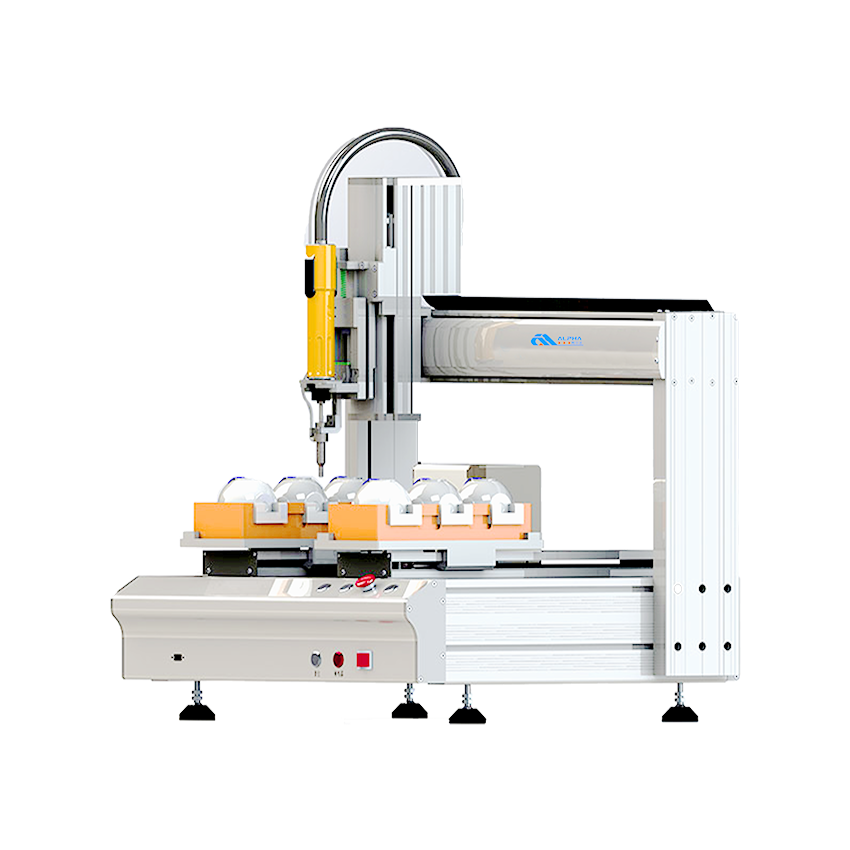
When the screws are neatly arranged, it enters the conveying stage. The screws are conveyed to the vicinity of the tightening mechanism through the conveying track. Conveyor tracks are usually composed of pipes or slide rails, and screws move forward within the tracks relying on gravity, air pressure or mechanical thrust. Some automatic screw machines adopt air-blowing conveying. By using the airflow generated from compressed air, screws are rapidly blown from the silo along the pipeline to the area below the screwdriver. This method is fast and suitable for conveying small-sized screws. Another type is the suction conveying, which uses vacuum suction to attach the screw to the screwdriver mouth and then performs the tightening operation. The suction type is relatively more stable and is suitable for larger or heavier screws.
The last step is to tighten the screws. The tightening mechanism is mainly composed of electric or pneumatic screwdriver heads. When the screw is conveyed to the selected position, the screwdriver head will descend and align with the screw head. Through the actions of rotation and downward pressing, the screw is screwed into the workpiece. The rotational power of a screwdriver head is provided by a motor or a cylinder. A motor-driven screwdriver head can adjust its rotational speed and torque by controlling the current, while a cylinde-driven one relies on air pressure to control the tightening force. During the tightening process, the machine will also be equipped with some detection devices, such as torque detection sensors. This sensor can monitor in real time the torque applied by the screwdriver head when tightening the screw. When the preset torque value is reached, the sensor will feed back a signal to the control system, which will then control the screwdriver head to stop working to ensure that the screw tightening degree meets the requirements.
In addition, the entire working process of the automatic screwdriver is uniformly scheduled by the control system. The control system can be a simple button operation panel or a complex programmable logic controller (PLC). The operator sets the parameters for screw tightening through the control system, such as the tightening sequence, torque size, and rotational speed. The control system will direct each component to work in coordination according to the preset program, achieving an automated process from screw supply, transportation to tightening. This replaces manual labor to complete the cumbersome screw tightening work, improving production efficiency and consistency.